
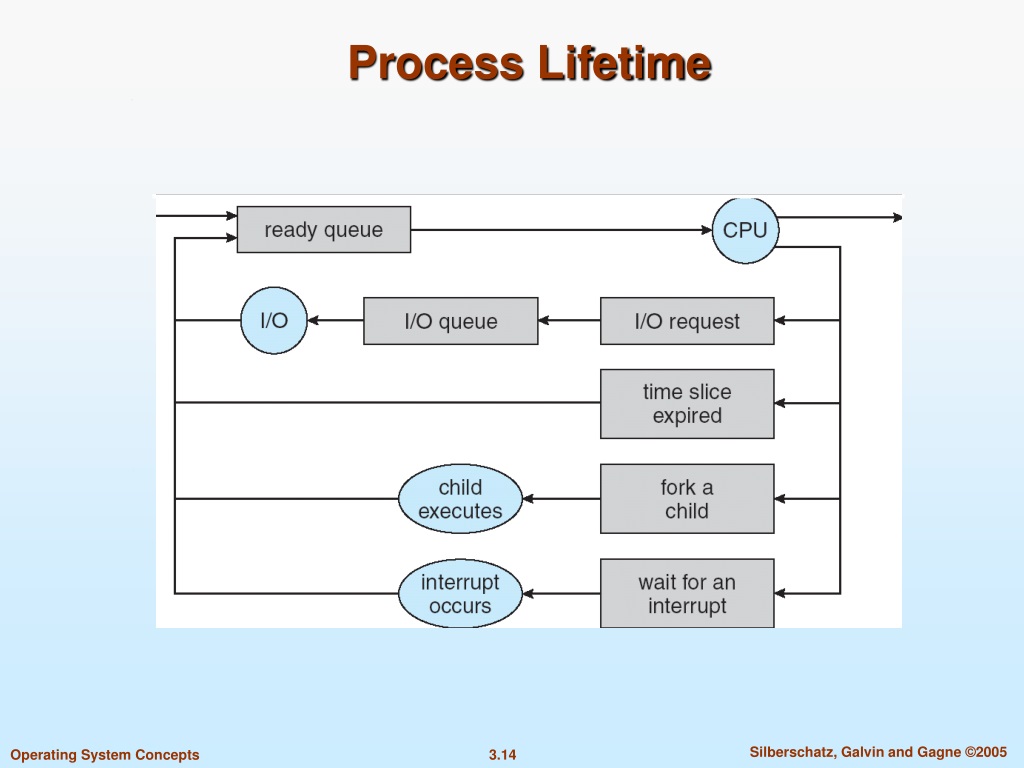
The Thinking Processes are optimized for complex systems with many interdependencies (e.g., manufacturing lines). The Theory of Constraints includes a sophisticated problem solving methodology called the Thinking Processes. This step is a reminder to never become complacent – aggressively improve the current constraint…and then immediately move on to the next constraint. Therefore, once a constraint is resolved the next constraint should immediately be addressed. The Five Focusing Steps are a continuous improvement cycle. In some cases, capital investment may be required. Normally, actions are continued at this step until the constraint has been “broken” (until it has moved somewhere else). If the constraint still exists (i.e., it has not moved), consider what further actions can be taken to eliminate it from being the constraint. Review all other activities in the process to ensure that they are aligned with and truly support the needs of the constraint. Make quick improvements to the throughput of the constraint using existing resources (i.e., make the most of what you have). Identify the current constraint (the single part of the process that limits the rate at which the goal is achieved). As shown in the following diagram, it is a cyclical process.
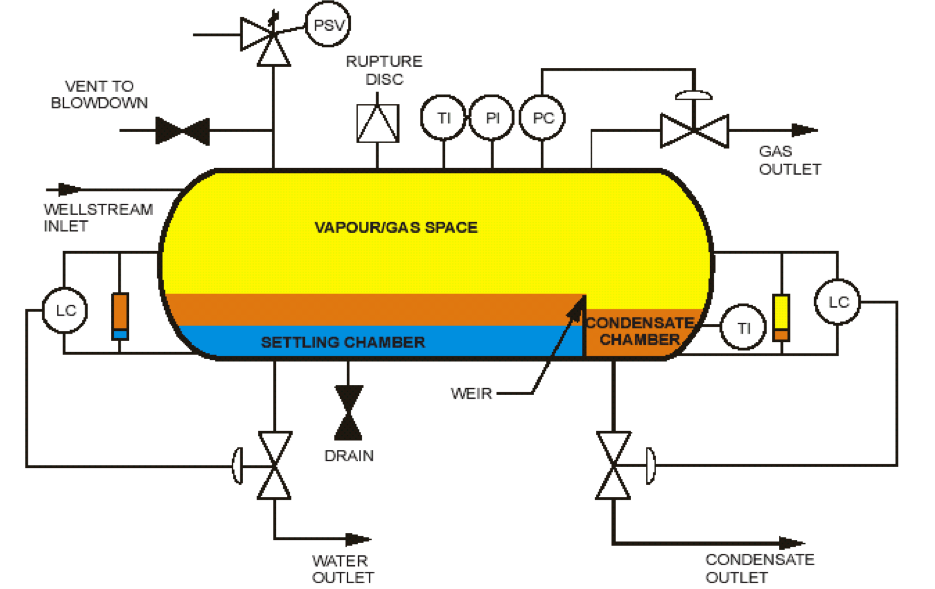
The Theory of Constraints provides a specific methodology for identifying and eliminating constraints, referred to as the Five Focusing Steps. In fact, Goldratt considers focus to be the essence of TOC. The underlying power of TOC flows from its ability to generate a tremendously strong focus towards a single goal (profit) and to removing the principal impediment (the constraint) to achieving more of that goal. Thus, TOC seeks to provide precise and sustained focus on improving the current constraint until it no longer limits throughput, at which point the focus moves to the next constraint. A very important corollary to this is that spending time optimizing non-constraints will not provide significant benefits only improvements to the constraint will further the goal (achieving more profit).
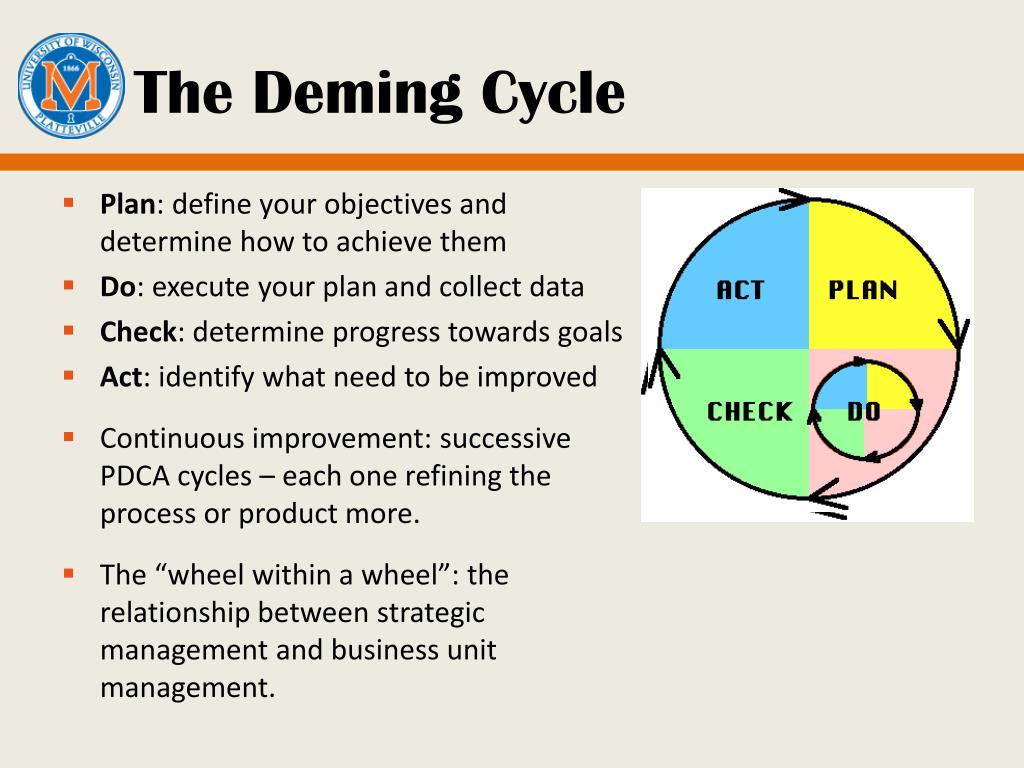
The core concept of the Theory of Constraints is that every process has a single constraint and that total process throughput can only be improved when the constraint is improved. Reduced Inventory: eliminating bottlenecks means there will be less work-in-process.Reduced Lead Times: optimizing the constraint results in smoother and faster product flow.Improved Capacity: optimizing the constraint enables more product to be manufactured.Fast Improvement: a result of focusing all attention on one critical area – the system constraint.Increased Profit: the primary goal of TOC for most companies.In environments where there is an urgent need to improve, TOC offers a highly focused methodology for creating rapid improvement.Ī successful Theory of Constraints implementation will have the following benefits: The top priority is always the current constraint. One of the appealing characteristics of the Theory of Constraints is that it inherently prioritizes improvement activities. Since then, TOC has continued to evolve and develop, and today it is a significant factor within the world of management best practices. Eliyahu Goldratt conceived the Theory of Constraints (TOC), and introduced it to a wide audience through his bestselling 1984 novel, “The Goal”. Throughput Accounting: a method for measuring performance and guiding management decisionsĭr.The Thinking Processes: tools for analyzing and resolving problems.The Five Focusing Steps: a methodology for identifying and eliminating constraints.The Theory of Constraints provides a powerful set of tools for helping to achieve that goal, including: So what is the ultimate goal of most manufacturing companies? To make a profit – both in the short term and in the long term. It hypothesizes that every complex system, including manufacturing processes, consists of multiple linked activities, one of which acts as a constraint upon the entire system (i.e., the constraint activity is the “weakest link in the chain”). The Theory of Constraints takes a scientific approach to improvement. In manufacturing, the constraint is often referred to as a bottleneck. The Theory of Constraints is a methodology for identifying the most important limiting factor (i.e., constraint) that stands in the way of achieving a goal and then systematically improving that constraint until it is no longer the limiting factor.
